Alloy Design
Additive Manufacturing
Optimus Alloys is designing alloys to achieve "printability-performance" synergy as detailed in the article by Mishra and Thapliyal (2021) on aluminum alloys. The initial attempts are for laser powder bed fusion additive manufacturing. The approach itself is amenable to different fusion based additive manufacturing techniques. Find out more at "Design approaches for printability-performance synergy in Al alloys for laser-powder bed additive manufacturing"
Friction Stir Additive Deposition
Friction stir additive deposition is a solid state additive manufacturing technique. It is commercially known as the MELD process, patented by the MELD corporation. All the three processes discussed on this web site represent disruptive manufacturing technologies. Optimus Alloys brings detailed metallurgical knowledge to support and advance these new technologies or processes.
Friciton Stir Welding and Processing
Friction stir welding has revolutionized the solid state welding of high strength aluminum alloys. It has been widely adopted by industry. Have you ever wondered that for each new alloy, sheet/plate thickness, alloy temper, your industry has to do process development! Optimus Alloys can help you with its predictive approach. This will help you cut down on the experimental effort and improve joint performance. Check out the book on "Friction Stir Welding and Processing" by Mishra et al. 2014.
Examples
Aluminum Alloys
Aluminum alloys provide the best opportunities for lightweight structures with or without topological optimization. Optimus Alloys is working on new alloy compositions that allow microstructural control and printability over a wide range of process parameters. See the article (Design of heterogeneous structured Al alloys with wide processing window for laser-powder bed fusion additive manufacturing) by Thapliyal et al. (2021) as an example of such an approach.
Copper Alloys
Copper alloys provide best opportunities for high performance conductors. Optimus Alloys is designing copper alloys with combination of high conductivity and strength for heat exchangers and other thermal management applications.
High Entropy Alloys
High entropy alloys are changing the paradigm of metallic alloys. Optimus Alloys is designing alloys that exhibit superior combination of properties and take advantage of hierarchical deformation mechanisms. Check out the fundamentals and potential of these alloys for enhanced mechanical properties in this overview article "High entropy alloys – Tunability of deformation mechanisms through integration of compositional and microstructural domains" by Mishra et al. (2021).
About Us
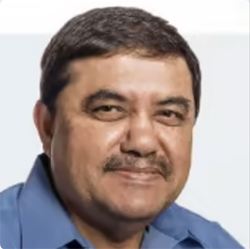
President - Dr. Animesh Bose
Dr. Animesh Bose has been involved in the area of powder metallurgy and particulate materials (PM) for more than thirty years. He has over 120 technical publications and currently serves as the VP of R&D, Desktop Metals Inc., a startup company involved in the area of 3D printing of metal parts. He is currently involved in process development for different metals and alloys by additive manufacturing. He has contributed in several areas of development, processing and manufacturing of advanced particulate materials. His areas of interest include the powder processing of advanced PM materials including refractory metals (especially tungsten-based) and their alloys, ferrous-based PM materials, hardmaterials, tungsten heavy alloys, intermetallic compounds, ceramics and metal matrix composites, and hot consolidation of high strength and high hardness materials.
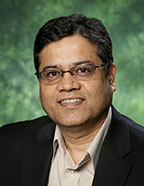
Chief Scientific Advisor - Dr. Rajiv S. Mishra
Dr. Rajiv S. Mishra (Ph.D. in Metallurgy from University of Sheffield) is a University Distinguished Research Professor at University of North Texas and founder of Optimus Alloys. He serves as the Director of a recently launched Advanced Materials and Manufacturing Processes Institute (AMMPI) at UNT. He is also the UNT Site Director of the NSF I/UCRC for Friction Stir Processing and a Fellow of ASM International. He is a past-chair of the Structural Materials Division of TMS and served on the TMS Board of Directors (2013-16). He has authored/co-authored 417 papers in peer-reviewed journals and proceedings and is principal inventor of four U.S. patents. His current publication based h-index is 71 and his papers have been cited more than 28000 times. He has co-authored two books; (1) Friction Stir Welding and Processing, and (2) Metallurgy and Design of Alloys with Hierarchical Microstructures. He has edited or co-edited fifteen TMS conference proceedings. He is an Associate Editor of the Journal of Materials Processing Technology and serves on the editorial board of Materials Science and Engineering A, Science and Technology of Welding and Joining, and Materials Research Letters. He is the founding editor of a short book series on Friction Stir Welding and Processing published by Elsevier and has co-authored seven short books in this series.
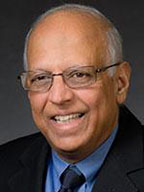
Scientific Advisor - Dr. Krishnan K Sankaran
Dr. Krishnan K Sankaran is a retired Senior Technical Fellow of The Boeing Company, where he worked for 36 years after receiving his Ph.D. in Materials Science and Engineering from the Massachusetts Institute of Technology in 1978. He is recognized internationally for his work in metallic materials and manufacturing technologies many of which were funded by US Navy, US Air Force and NASA, and have been implemented successfully in aerospace systems. Dr. Sankaran is presently an Adjunct Instructor in the Department of Mechanical Engineering and Materials Science at Washington University in St. Louis, where he teaches a course based on the book titled “Metallurgy and Design of Alloys with Hierarchical Microstructures” (Elsevier, 2017), which he co-authored with Dr. Rajiv S. Mishra of University of North Texas (UNT), Denton, TX. Dr. Sankaran is also an Adjunct Professor in the Department of Materials Science and Engineering at UNT. He has published a book chapter and several papers in peer-reviewed journals and has four US patents.